
plastic wrap
Learn more about plastic film recycling and its benefits.

nonwoven bags
Discover the environmentally friendly benefits of nonwoven bags.

artificial turf
Explore the sustainability of artificial turf solutions.

BOPP film
Understand the recycling process of BOPP films.

mulch plastic film
Learn how mulching plastic film contributes to agriculture.

woven bag
Learn more about the durability and recyclability of woven bags.
Our process
pre-washing and sorting
Large contaminants are removed and materials are prepared for optimized processing in subsequent stages, increasing overall efficiency.
granulation
The materials are evenly reduced in size to allow for more effective cleaning and preparation for recycling.
Intensive Hot Cleaning
High-temperature cleaning combined with precise chemicals removes oils, adhesives and stubborn contaminants from PE films and fabrics.
separation and filtration
Advanced separation removes light impurities and isolates high-quality plastic materials for further processing.
flushing and drainage
Thorough rinsing and efficient dewatering prepare the materials for the final drying phase and ensure optimal cleanliness.
Thermal drying
The materials are thermally dried to achieve low moisture content, resulting in high quality output ready for use in advanced applications.
single-shaft shredder Technical data
The single shaft shredder is designed to efficiently shred and reduce the size of a wide variety of materials such as plastics, wood and general industrial waste.
- Rotor speed: 60-100 rpm
- Blade material: High-strength alloy steel or D2 steel
- Cutting chamber: 400mm x 500mm to 2000mm x 2000mm (depending on model)
- Screen size: 40mm – 100mm (adjustable)
- Engine power: 15-200 kW
Main functions:
- shredding of various waste materials
- Preparation of materials for recycling
- Reducing material size for easier handling
- Reducing dust formation and improving operating equipment
- Increase blade durability and overall machine life

wet plastic granulator Technical data
The wet plastic granulator is an improved version of our universal granulators, designed for the efficient cutting and pre-cleaning of plastic bottles, films and rigid materials.
- Rotor speed: 400-600 rpm
- Blade material: D2 high-carbon, high-chromium steel
- Cutting arrangement: V-shape or double scissor blade
- Screen size: 10mm – 100mm (adjustable)
Main functions:
- cutting plastic materials
- Pre-cleaning and loosening of impurities
- Reducing dust formation in recycling plants
- Extending the life of the blades and the machine
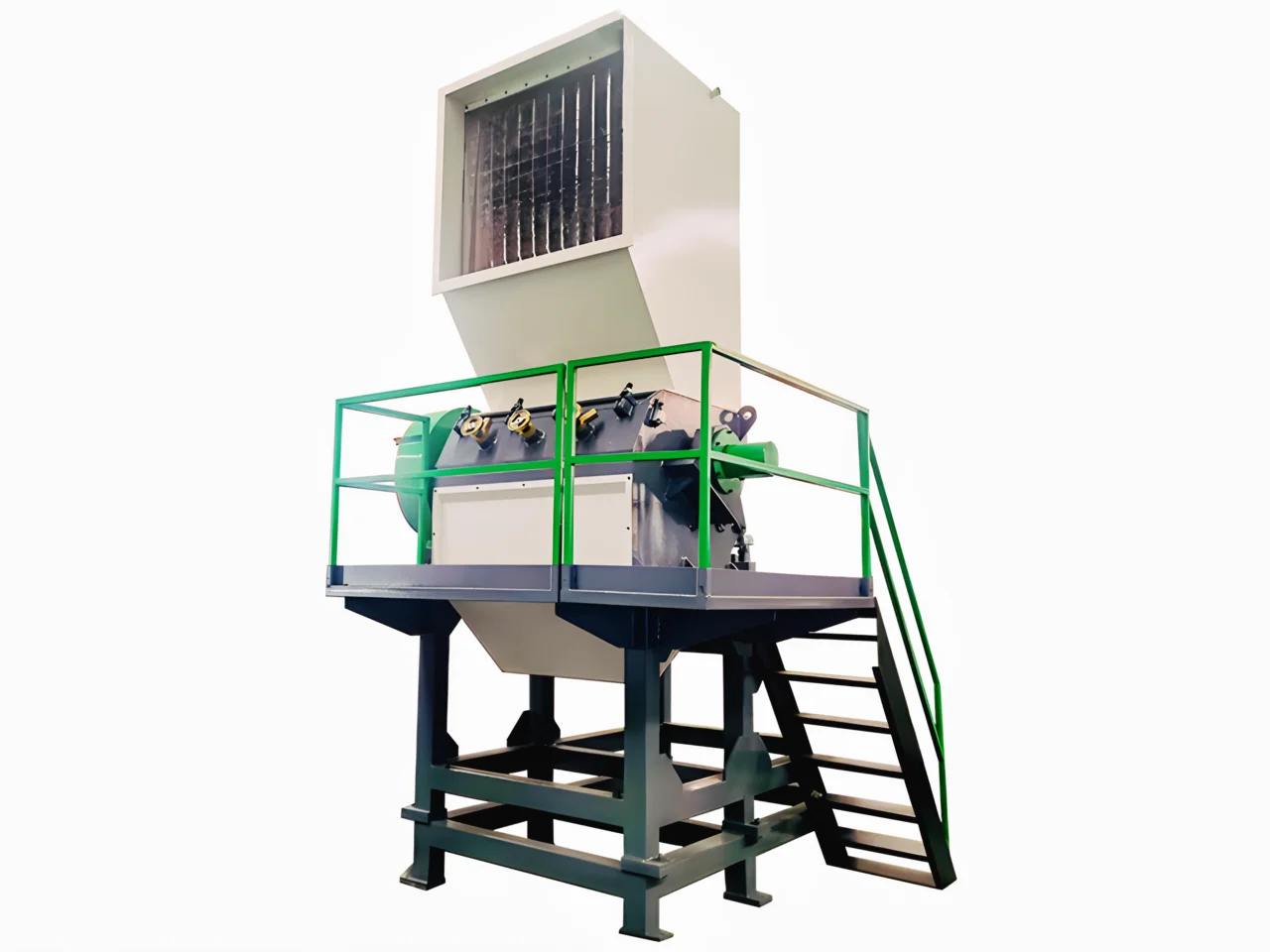
friction washer system Technical data
The friction washing system is designed for the efficient cleaning and transport of plastic flakes, films and recycled materials.
- Rotor speed: 500-600 rpm
- water system: upper inlet, lower outlet
- Operation: Continuously
- Cleaning method: friction-based
Main functions:
- cleaning of plastic materials
- Transport of materials between machines
- removal of soil, sand and other contaminants
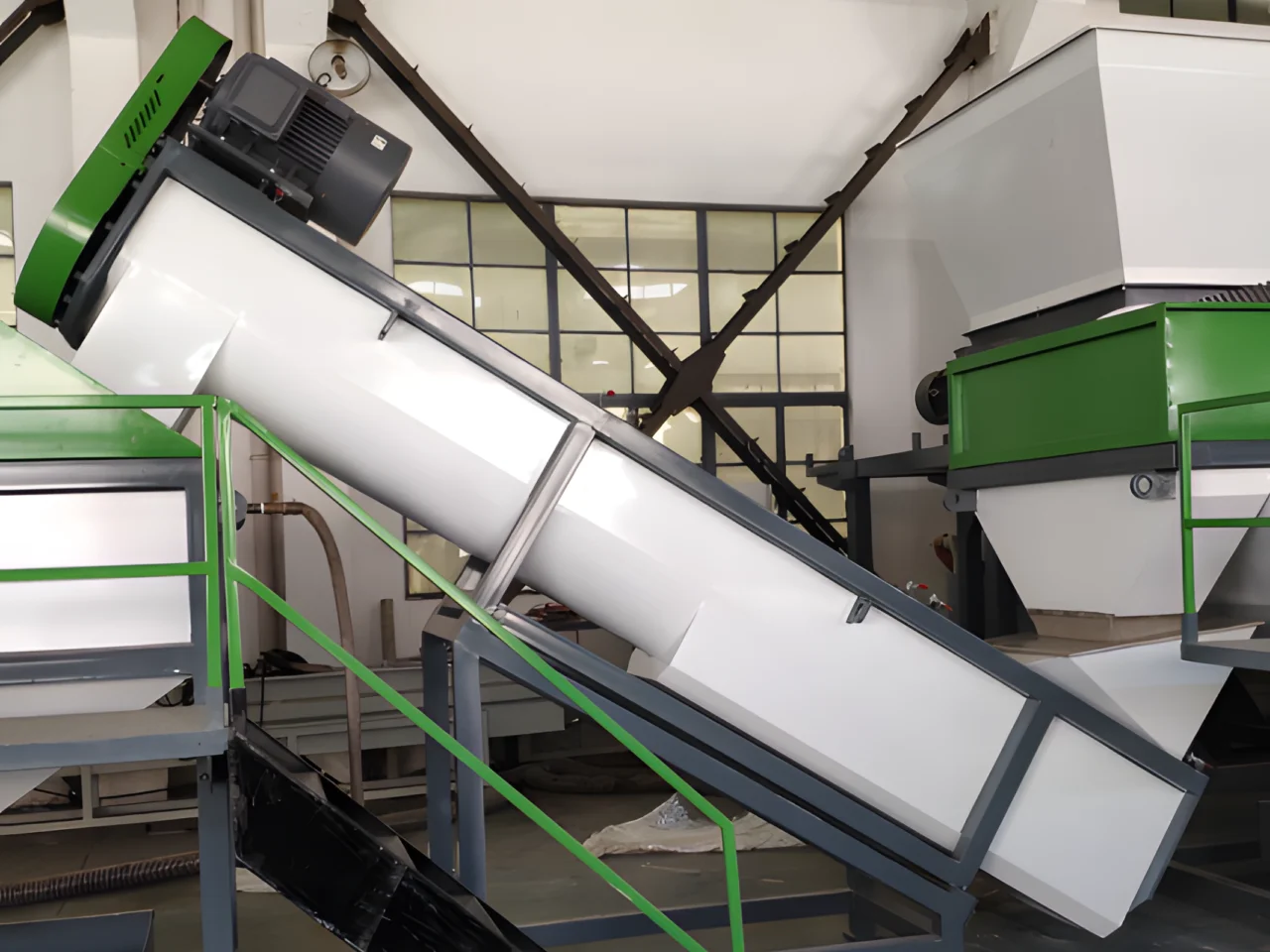
floating separation water tank Technical data
Our Floating Separation Water Tank is designed to efficiently separate PP and PE plastics from mixed streams while simultaneously cleaning the materials for further processing.
- inner width: 1000mm – 1800mm
- Total length: 4 – 7 meters
- Inner material: Type 304 stainless steel
- outer frame: carbon steel
- Paddle motors: 1.5KW*2 (frequency control)
Main features:
- "W"-shaped bottom for improved efficiency
- Two-piece construction for better contamination management
- Water-based separation for PP and PE plastics
- Simultaneous cleaning and separation
hot washer Technical data
The hot washer is specifically designed for cleaning plastic films and fabrics with oil spills, adhesives and other stubborn contaminants. It features an integrated heating system that eliminates the need for an external steam generator and ensures effective cleaning with optimized chemicals.
- Operating mode: Continuous or batch mode (customizable)
- heating system: Integrated electric heating
- Washing method: hot water bath with chemical additives
- Suitable materials: PE films, fabrics and other contaminated plastics
Main features:
- Effective removal of oil spills, adhesives and stubborn contaminants
- Integrated heating system that eliminates the need for an external steam generator
- Optimized use of chemicals for improved cleaning
- Flexible operating modes that meet different process requirements
- Robust construction for continuous, demanding operation

Centrifugal dryer dewatering Technical data
Our centrifugal dryer dewatering machine is a highly efficient, energy-efficient equipment designed to partially remove water from plastic materials using centrifugal force. It is an important first step in PE film and PET bottle washing lines.
- speed: Approximately 1,000 rpm
- Moisture reduction: At about 20-30%
- Main components: Long shaft with straps, wire mesh tunnel
- Housing: metal container with external electric motor
Main features:
- High efficiency with low energy consumption
- Processes material with high water content
- Suitable for PET flakes, PP/PE films and other plastic regrinds
- Patented design that also serves as a friction washer for cooling and cleaning
- water recyclability
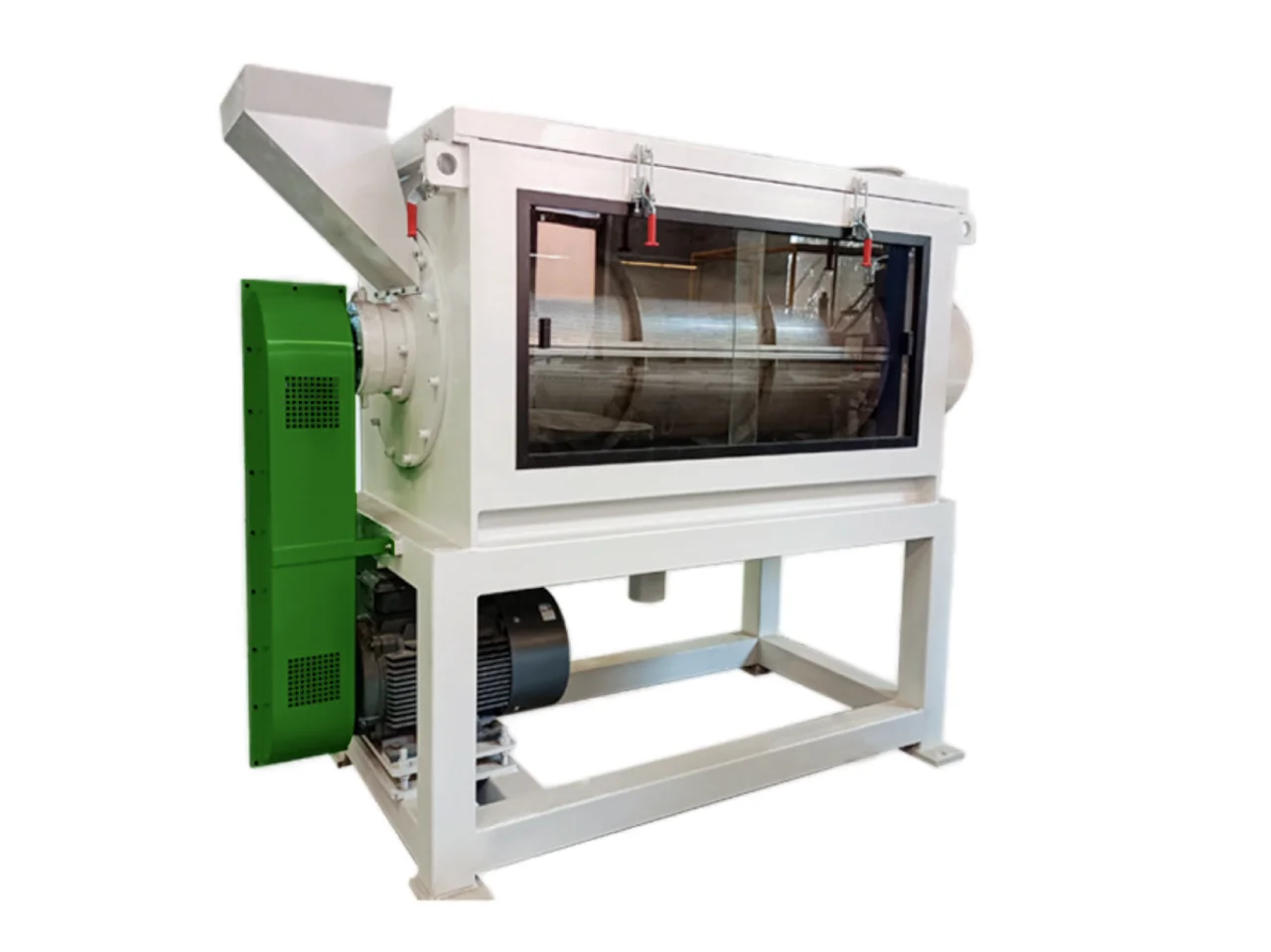
pipe dryer Technical data
Our tube dryer is designed for efficient moisture removal through dehydration and is ideal for plastic film and PET washing lines. It is an important final step to reduce moisture content to below 3%.
- Model: RSJ800
- Wind instrument performance: 5.5 KW
- Heating power: 36 KW
- Pipe diameter: ⌀159mm
- Pipe material: stainless steel type 304
Main features:
- Continuous drying process
- Integrated cyclone separator
- hot air dehydration system
- Efficient removal of dust and fine dust
- Scalable design (can use multiple units in series)

Film Squeezer Technical data
The Film Squeezer, also known as Squeezer Drying Machine, is designed for the efficient dewatering and compaction of washed plastic films, including polyethylene (PE) and polypropylene (PP). This machine is indispensable in recycling lines and significantly reduces moisture content as well as material volume to optimize downstream processing.
- Moisture reduction: Reduces moisture content from 10-35% to 1-5%
- squeezing mechanism: screw compression system
- Output capacity: 300 kg/h – 1500 kg/h (varies depending on model)
- Energy consumption: 75 kW – 162 kW
Main functions:
- Efficiently reduces moisture content and prepares materials for extrusion pelletizing
- Compresses film flakes into solid lumps for higher density and stability during extrusion
- Increases overall recycling efficiency by delivering drier and denser materials
- Durable construction ensures long life and reliable performance under heavy-duty operation

advantages of our technology
Environmentally friendly
Reduced water and energy consumption, minimizing environmental impact.
High output quality
Excellent cleaning for highly recycled materials, guaranteed first-class results.
Versatile
Capable of processing various rigid plastics, offering unparalleled flexibility.
Contact us
Ready to improve your plastic recycling capabilities? Contact our team of experts today for a customized solution.
Get a quote